A process is necessary for the division of labor because the task isn’t just in one person’s head anymore.
The full-stack engineer might be a fine person to write the process, but shouldn’t be running it from start to end alone — the job is 240 times more efficient when it’s split up amongst pin specialists: the person who cuts pin wires all day is less fallible than the solo pin master craftsman. Let’s stop talking about pins.
On a winter morning in 1907, Henry Ford took Charles E. Sorensen to Piquette Avenue Plant, an empty building in Detroit that would go on to become the birthplace of America’s first mass-produced affordable car. “We’re going to start a completely new job” he told the head of production.
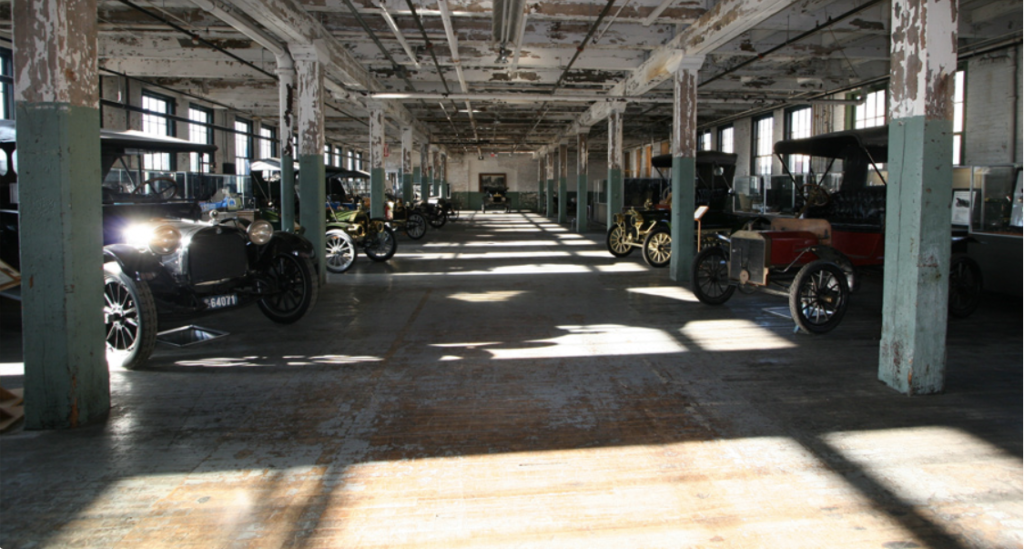
The Piquette Avenue Plant in Detroit, Michigan. The site of the world’s most influential business process implementation.
Ford explained his idea for a new process. Instead of one artisan creating a product alone, everyone was taught to do one of 84 simple, repetitive jobs. With this new approach to processes, Ford cut the manufacturing time of the Model T down from 12.5 hours to 2.5 hours.
Not only was that a triumph for Ford’s bank account, it was one of the most revolutionary moments ever to occur, not just in the history of cars or manufacturing, but in the entire history of business.
Do you have any interesting anecedotes on process impact? Please do comment.